Galvamétaux
A true Odoo success story!
Galvamétaux, a leader in the hot-dip galvanizing of small metal parts, recently took a giant step towards operational efficiency with the implementation of Odoo.
Galvamétaux : Behind the scenes
Pierre Grégoire, Technical Director at Galvamétaux, opened the doors of their company to reveal the secrets of their transition to Odoo.
With over 50 years of expertise, Galvamétaux is a major player in its sector, shipping around 25,000 tonnes of metal parts a year across Europe. Today, with nearly 40 employees, the company continues to expand and prosper internationally.
But before we dive into the details of their digital transformation, let us briefly explain what hot-dip galvanizing is in a nutshell. Hot-dip galvanizing is a metallurgical process in which a protective zinc coating is applied to metal parts to protect them from corrosion. The process involves dipping parts in a bath of molten zinc, creating a stronger, longer-lasting metallurgical bond.
And rest assured, if you were in the dark about this definition before you heard about Galvamétaux, you're not alone!
The challenge
Given its constant evolution, Galvamétaux found itself faced with the classic challenges of a fast-growing company: the need to modernize its management system, and the desire to unify its various processes in a centralized system. The diversity of its operations, from the production of small metal parts for various sectors to complex inventory and order management, called for a solution capable of simplifying, automating and optimizing all internal processes.
This is where the implementation of Odoo ERP software comes in, with strategic and operational support from Niboo.
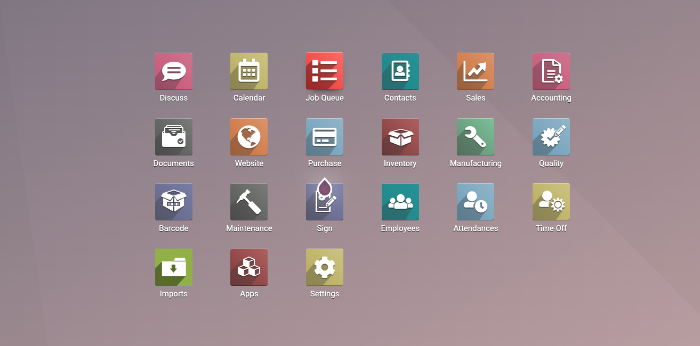
The Odoo solution: a strategic choice
The transition to Odoo as a new ERP system was a well-considered decision for Galvamétaux.
Attracted by its flexibility and ability to adapt to the company's specific needs, Odoo emerged as the ideal solution for the complex operational challenges of daily business.
Pierre Grégoire played a key role in this strategic decision.
Having heard so much positive feedback about Odoo from my professional network, the choice of this management system was an obvious one. However, beyond the online recommendations, it was the human dimension that really tipped the balance in Niboo's favor. The warm exchanges and convincing meetings with the Niboo team confirmed our choice of collaboration.
Discover the success story on video !
We integrated standard modules and customized developments to transform their operations, centralize, digitize and optimize their entire process.
Implementation and customization
Galvamétaux now benefits from the seamless integration of various Odoo modules, including sales, accounting, purchasing, manufacturing and inventory management. These modules work in harmony to provide a detailed view of operations, from order tracking and customer service to production monitoring and quality control, all centralized in one easy-to-use platform.
In partnership with Niboo, Galvamétaux was able to customize and deploy these key Odoo modules.
Pierre Maloteau, Business Analyst at Niboo in charge of the project, explains:
The project at Galva Métaux proved to be an exciting and rewarding challenge for the whole team. Adapting the Odoo modules to the specifics of their business required a tailored approach, including the development of a specialized connector to facilitate communication between the galvanizing machines and the ERP. This innovation enabled seamless integration of data in real time, essential for precise management of Galva Métaux's unique transformation process. The efficiency of this customized solution now ensures complete traceability, from the arrival of raw materials to their final transformation, reinforcing our commitment to meeting the unique needs of each customer.
Concrete examples of everyday use
On a day-to-day basis, Galvamétaux uses Odoo to keep precise track of each production phase.
For example, the sales module provides a complete history and traceability of each production run. It uses galvanizing data (production time, quantity delivered, thickness measurements, coating) to enrich order forms, offering total transparency to customers. Data collected from scales at the end of production is automatically integrated into the system, reducing errors and speeding up the invoicing process.
The stock module comprises several blocks:
- Receiving
- Internal transfers
- Deliveries
- Returns
- Manufacturing
It also illustrates the efficiency of Odoo, facilitating verification of completed production quantities and tracking deliveries in real time. This automation ensures that Galvamétaux can respond quickly to customer requests while maintaining strict control over its inventories.
Tangible day-to-day benefits
Increased operating efficiency
Centralizing processes in Odoo eliminated redundancies and simplified workflows, resulting in a significant reduction in the time and effort required for administrative and operational tasks. Order management, from production to delivery, has become much smoother, accelerating the sales cycle.
Improved data accuracy
The direct integration of data, such as that from scales at the end of production, has considerably reduced manual input errors. This increased data accuracy enables Galva Métaux to offer its customers reliable and transparent information on their orders.
Real-time visibility
Thanks to Odoo's customized dashboards, employees at Galva Métaux now have a real-time overview of the status of operations, inventory and finances.
Optimizing inventory management
The inventory management module has transformed the way Galva Métaux manages its raw materials and finished products. This ensures better availability of products to meet customer demand.
Greater flexibility and adaptability
Odoo has given Galva Métaux the flexibility to adapt quickly to changes, whether in customer demands, market fluctuations, or the introduction of new production processes.
Improved customer satisfaction
Improved operational efficiency, data accuracy and transparency have led to a significant increase in customer satisfaction.
Conclusion
The adoption of Odoo at Galvamétaux marked a significant turning point, responding effectively to operational challenges and laying the foundations for constant evolution towards innovation and excellence.
Pierre Grégoire shares his enthusiasm for the future:
We look forward to the next steps in our digital journey, including the enhancement of the purchasing module for dynamic, real-time inventory management, and the optimization of manufacturing order planning. These advances represent not only a lever for growth, but also a means of further refining our operational excellence.
At Niboo, turning challenges into opportunities and propelling companies to new heights is at the heart of our expertise.
Contact us to explore together how we can facilitate your digital ascent and help you realize your full potential.
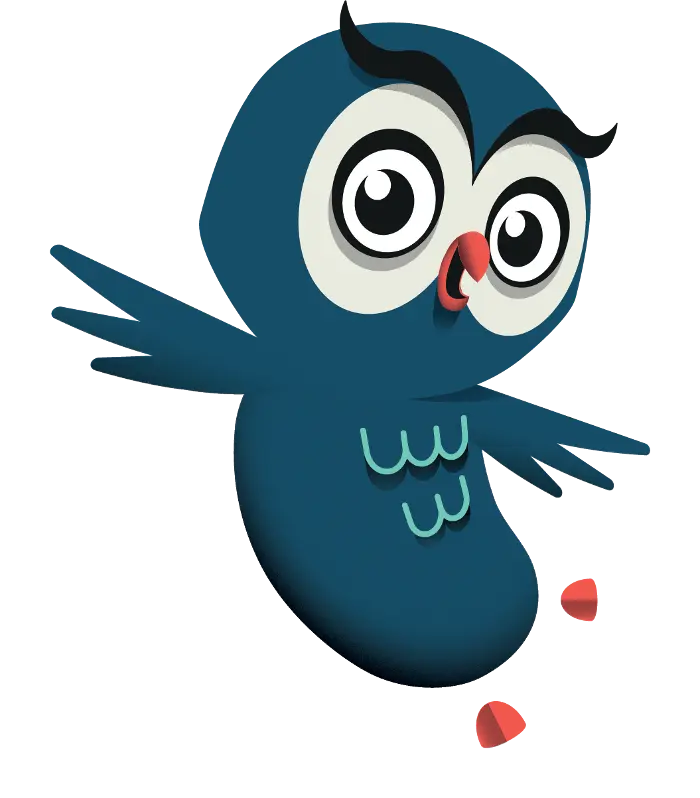
Optimize your business management today!
Increase your company's productivity, contact our experts for advice and a customized demo.